FEATURES
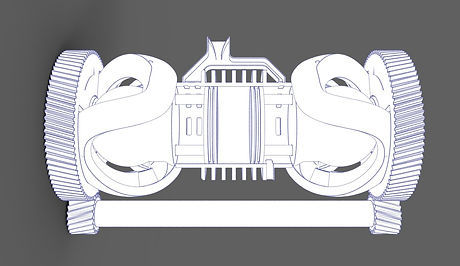
PERFECTLYÂ BALANCED, MOST POWERFUL
History of engines has seen many attempts about axial engines, opposed pistons engines, clean two strokes: but they had issues about incumbrance, mechanic friction, gas leakages, overheating, fuel providing.Â
CONVEE has been studied to collect all of said advantages, without relative flaws: its design grants feasibility, high power to weight and to volume ratios, and balance within each couple of cylinders.
CLEAN COMBUSTION TWO STROKE
CONVEE is a two stroke with efficient uniflow scavenging of the combustion chamber, and a dedicated space for air suction behind each piston. Such space is separated from lubricated parts with durable sealing already available on the market, so that combustion doesn't involve lubricant burn, with NO need of external blowers nor superchargers.
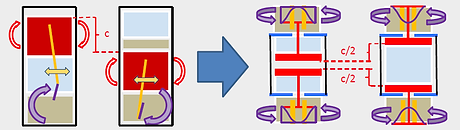
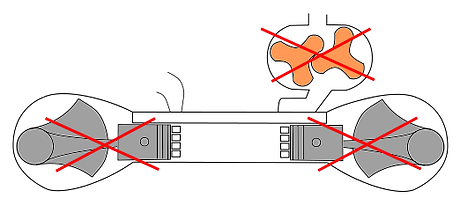
NO CONNECTING RODS AND SHORTÂ SKIRTS
The mechanism moving the pistons does not include long and unbalanced connecting rods, avoiding forces that tend to tilt the piston. This is why CONVEE's pistons don't need a long skirt, have minimum friction on cylinder's liner, and overall assembly is so small.
OPTIMIZED THERMODYNAMIC CYCLE
Usually a crankshaft moves pistons with a function in time similar to a sinusoid, but combustion in CONVEE can completely happen at minimum volume (TDC); the following expansion can be faster, then closer to the adiabatic also granting high torque, being the push more tangent to cams rotation direction. Heat exchange through two pistons in each cylinder allows both suction and compression to be more isothermal: efficiency is then highly improved.


DURABLE SPHERICAL CAM DESIGN
The second patent about CONVEEÂ involves the use of spherical cams instead of cylindrical cams.
Swinging arms hinged at the center of a spherical cam terminate with conical bushings, rolling on spherical cam tracks and never sliding tangentially nor radially, having always a perfect contact along a radial line between bushings and cam tracks, avoiding any friction wear.
SIMULATIONS RESULTS
Gasdynamics simulations showed involved stresses, which proved structural feasibility, beyond confirming the foreseen gain in efficiency and power.
A 0.5L engine may develop 100hp, with stable highest torque all along RPM range of use.
